1 August, '07
At this stage of building there are few of the spectacular
changes to the boat's appearance that occur when planking up
or fitting decks. The pieces being fitted are small and there
is much finishing work happening. Things like electrical wiring,
water tankage and piping, fitting up the cabin heater fuel tank
etc are all things that contribute to the boat's progress but
they are not much to look at and photos of this sort of thing
are hard to make exciting.
However, we have just had a really good day watching foundryman
Roger Woodhouse making Resolution’s cast bronze fittings.
Charlie had spent a couple of weeks making the patterns from
my drawings, using MDF sheet, five minute epoxy and car body
filler it took a while but he made a light wooden (sic) replica
of each item needed. We took those over to see Roger to make
sure that they would be able to be used for making a mould,
and to get an estimate of the costs involved.
Roger
at the furnace, roaring away under the pressure of a big
air blower and seriously hot. This photo does not give
much of an indication of its sheer energy and heat, a
good place on a winters day.
|
The melted bronze, it looks quite beautiful,
but don’t be fooled this is unbelievably hot. |
The first estimate was a shock, a lot more money than we thought
, but after some negotiation and a change to a less expensive
metal brought that back to a workable level and Roger issued
an invitation to come over and watch as he did some of the pour.
We arrived to find the furnace roaring away and several bars
of what looked like pale gold ready to feed into the crucible,
a double row of two layer steel boxes full of black sand lined
up on the floor and Roger busy pressing the stemhead fitting
pattern into an other box. Some of the patterns are quite challenging
from a foundryman’s point of view, thin sections connecting
with thick ones, tight radius intersections and deep thin sections
that could only be set edge on into the mould.
Roger's great; he’d thought it over and figured out
how to do it. My homework (read several books that I found in
the library) seemed to have been helpful as no modifications
to patterns were required plus a large dose of his skills made
for a successful day.
It was quite spectacular to watch, the roar, the heat and glow
radiating from the furnace is quite something even in this small
operation, the careful handling of the “pot” full
of glowing hot metal that is so liquid it flows like water,
the heat radiating off it is such that you could grill your
steak from several paces away and the whole thing looks like
the inspiration for some of the underground volcanic scenes
from Lord of the Rings.
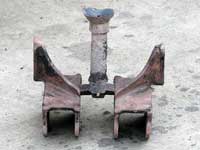
The two bow roller fittings, the bit that
is joining them is the pathway for the metal to follow
through the sand mould to fill the space that when hardened
becomes the moulded part. All that gets cut away and remelted
for another part.
|
The cranse iron for the end of the bowsprit,
deck pads, and a bar of the original metal. Good strong
fittings, custom made for the job, at a lot lesser price
than you’d find them in a shop for. A very worthwhile
exersize. |
Roger and his helper wheeled the crucible over to the moulds
(yes there is a proper name for them but foundry terminology
is not something that I am familiar with and you all know what
I mean) and literally just poured it in. This is metal, tough
metal, and watching it being poured in like water from a tap
is quite something. We stood well away, just in case, our light
shoes are not the thing to cope with spilled molten metal.
A while later a mould was picked up and split, shaken out and
the castings pulled free from the sand. Even sitting on the
concrete floor they had an air of solidity about them that the
wooden patterns did not have. I can tell you that if you are
building one of these, then there is no need to make the patterns
a little heavier ( for strength ) than I have drawn them. These
are strong, they have quite a reserve and while I had calculated
the strengths it's quite different to see the real thing.
Another stage of the build done. There is a lot of cleaning
up, drilling and countersinking and polishing to do, but it's
more progress.
Fun? You bet, it feels quite primal, casting metals.
John Welsford
Designer
Photos by Charlie Whipple
|