15 July, '07
I was up on the port side deck of Charlie’s Sundowner
last week. He handed up a glue spread sheet of ply and we lined
it up ready to screw it to the first layer of ply that makes
up the laminated plywood cabin top. It’s a landmark sort
of time in the building of the boat when that is completed,
the cabin feels cozy and secure, the view from the cockpit is
over the smooth curve of the cabin top to the foredeck and one
can almost see the dark green background of the mountains in
behind the gleaming white beach and swaying palms as the little
boat rolls down the tradewind swells. Sigh!
I like sitting in that cockpit, and was very pleased to be
able to take a prospective Sundowner builder up there and sit
him comfortably in the deep and sheltered cockpit while he looked
around eyes wide at the amount of space and comfort in this
little cruiser, only about 2 ft longer and a foot wider than
his own trailerable yacht. He climbed around down below, asking
why and how about key features, moving about to get a feel for
the space and I can imagine that he will be seeing the same
sort of images of cruising destinations in his minds eye that
I do when sitting in there looking out with unfocused eyes and
wandering mind.
She’s coming along. Charlie is busy making the patterns
that will go off to the foundry to be pressed into the sand
making the moulds into which the molten bronze will be poured
making the rough pieces that after a lot of filing, drilling
and grinding will become finished fittings ready for the boat.
Around the cockpit area he has completed the quarterdeck and
the area around the stern end of the cockpit. There are two
mini sampson posts there. We have jokingly called them “Delilah
posts“ as we have a bigger Sampson post up in the bow
and we have all three so well braced that any one of them could
support the entire weight of the boat. These after ones are
not only there to provide tie up points for the mooring lines
but they have to cope with the stresses of lying to a parachute
anchor in a serious storm, or dragging warps so they need to
be tough. More Kwila, one of the strongest of woods, and able
to cope with harsh environments without paint or varnish to
protect it.
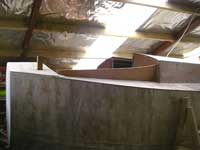
|
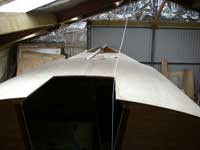 |
That quarterdeck has a hard point built in that will be drilled
and fitted with a hardwood pad that will mount a vice when needed.
It’s at the right height to be able to attack a metal
bar with a hacksaw, to spice a piece of wire rope or to hold
a piece while shaping it with a file or chisel. A good workshop
should have a vice, solidly mounted and accessible and a small
boat that is going to be going where Charlie is planning to
take Resolution really needs a good workshop. It’s a long
way to go to find someone who can fix it for you so it’s
all DIY and the cockpit will be a maintenance center, a woodworking
shop, a rigging shop and an engineering works as well. So, a
vice, a hardwood pad where things can be hit with big hammers,
where the skipper can swing a spanner or big wrench, or chop
with a chisel, is not only useful, it’s essential.

|
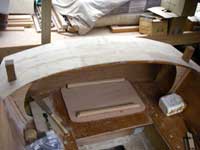 |
Much of this boat is two layers of wood laminated, the hull
itself, cabin sides, cabin top, decks and quarterdeck are all
done this way. As each part of the boat gets fitted and glued
up she gets more and more rigid. Now that the “lid”
is on she feels incredibly strong, reassuringly so and it’s
a feeling that’s very comforting when the immensity of
the planned voyage is considered. Hey, it’s big water
out there and deep in the Southern Ocean, about half way from
New Zealand to Cape Horn is the spot which is the most distant
from land that it’s possible to get on this planet.
I think I prefer the coconut palms.
John Welsford
Designer
Photos by Charlie Whipple
|